The unipolar stepper is a 50-percent efficient type of two-phase stepper motor. The unipolar stepper motor has two windings for each phase to allow the electrical current to flow in only one direction in each winding. This is opposed to the single-winding-per-phase construction of a bipolar stepper motor, which requires that the electrical current flows in both directions. The unipolar stepper motor is designated as having 50-percent efficiency because it uses twice the amount of wire as a similar-sized bipolar stepper motor but energizes only half of the windings at any one time.
This type of stepper motor has the simplest schematic of all two-phase stepper motors. Each phase of the unipolar stepper motor consists of two windings with a common ground, resulting in three leads per phase. In the majority of cases, the common ground leads of the phases will be paired inside the motor, resulting in five external leads for a two-phase unipolar stepper motor.
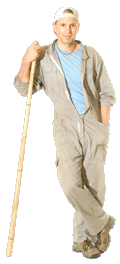
With the controlled energizing of the windings via a controller circuit, the unipolar stepper motor circuit does not require the brushes used by motors powered by direct current (DC), and the direction of the shaft's rotation can be changed easily. Using an external controller circuit, the energizing cycles of the windings can be timed to allow the unipolar stepper motor to move forward or backward a precise number of steps. When combined with other technology, the unipolar stepper motor can be used for the creation of home robotics, arduino-controlled projects and other projects that require precisely timed, angular movements.
As the unipolar stepper motor's windings are energized individually using a controller circuit, the individual windings become magnetically charged. This electromagnetic charge pulls the teeth of the gear toward the winding and within range of the next winding. At this point, the current to the first winding is cut off by the controller circuit and directed to the next winding in the series. As the current is switched from one winding to the next, the teeth of the gear follow the magnetic field, making the step to the next winding where the gear will rest until the process is repeated or reversed.
In a stepper motor, the speed, torque and direction of movement are controlled by the controller circuit, giving these motors a wide range of capabilities. The stepper motor functions in individual steps, so rather than the smooth rotation of a DC motor, it produces more noise and vibration than comparably sized DC motors. On the other hand, the unipolar stepper motor requires less maintenance because there are no brushes to wear out, and it produces controlled, variable movements that are not possible with a DC motor.