A slump test is a method used to determine the consistency of concrete. The consistency, sometimes described in terms of stiffness, generally indicates how much water has been used in the mix. The test allows builders and construction crews to get a good sense of how the mixed product will perform in a variety of settings, and also gives them the opportunity to add either more powder or more water in order to get the right balance. Different projects have different specifications when it comes to concrete stiffness, and testing the results is usually a lot more accurate than simply following prepared instructions or making informed guesses.
Proportion Variables
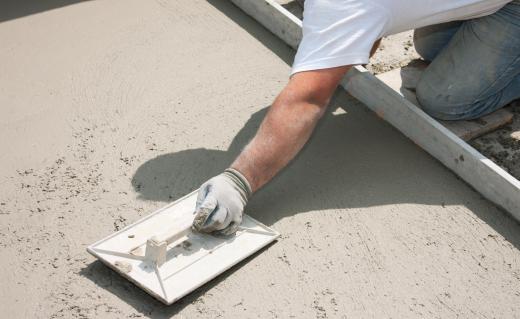
Concrete generally starts out as a powder, and in almost all cases comes as a combination of aggregate, which is gravel and sometimes also sand; cement; and water. The proportions of the mix can be varied depending on the source and manufacturer, though, which can make it difficult to simply guess or measure with precision. A larger proportion of water causes a softer, wet concrete mix, which is easier to handle during the pour and requires less care during curing. It also results in a slightly softer and less durable finished product. A smaller amount of water causes a stiffer, wet concrete mix, which is harder to manage but makes a stronger and more durable finished product that is capable of bearing more weight.
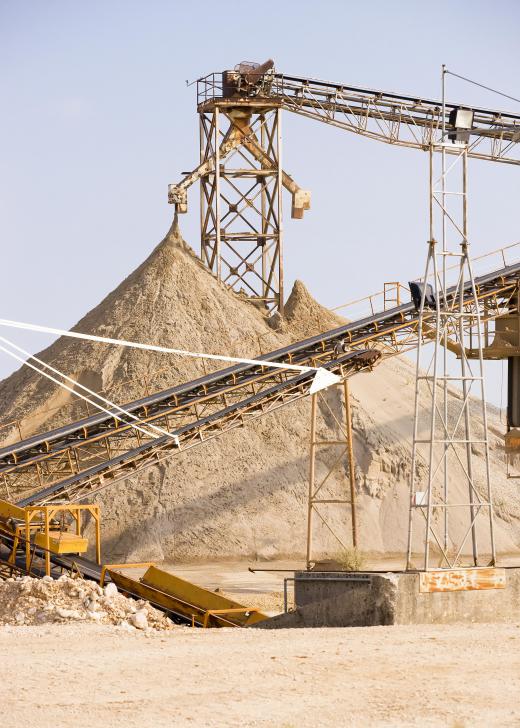
Contractors typically order wet concrete with a slump rating suitable for the job they’re trying to do, which means that they tell the supplier what sort of proportions and ratings they’re looking for. Ideally the mixed concrete comes to the site ready to pour, but in most cases builders and others will want to test it before getting to work. Slump tests at delivery are a good way to double-check stiffness, since it’s a lot easier to send a load back than it is to un-pour it if it works out to be too watery or too dense.
How the Test Is Performed
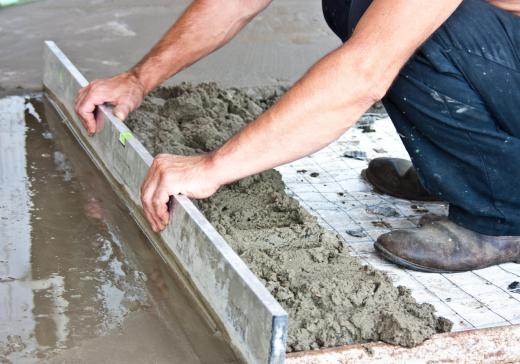
Manufacturers typically perform the slump test by filling a specialized test mold with wet concrete. In most cases the mold is shaped more or less like a cone that is missing its pointed end. A 5/8-inch (1.5 cm) diameter metal rod is inserted into the filled cone and pumped up and down about 25 times, mainly to remove air bubbles and settle the concrete. Anything that is spilling over the top of the mold should be leveled off, and then the mold is generally removed; without the support from the mold, the concrete slumps down under its own weight. The amount of slumping is the most important thing.
The rod is then usually placed horizontally over the slumped pile of concrete and balanced on the empty mold, which most measurers will set nearby. A ruler is used to measure the distance between the rod and the concrete, which represents the height lost when the concrete slumped down. This number is the “slump” for that particular batch of concrete.
Rating Specifications
In most cases, a slump of 1 to 3 inches (2.5 to 7.6 cm) indicates a very stiff mix and is the most suitable for commercial work. This is sometimes expressed as "1 to 3" on packaging and in sales information. A stiff mix like this can be really difficult to work with, and ordinarily it requires a mechanical vibrator to get it to consolidate properly. It generally produces the hardest and strongest concrete.
A slump of 4 or 5 inches (10.1 to 12.7 cm) is generally thought to be the most appropriate for residential work, and pouring concrete is easier with this amount of slump. This sort of material can usually be worked by hand, and it still results in strong concrete in most cases. Most experts say that a slump greater than 5 is usually too runny to work with, and with few exceptions a mix with a slump of more than 7 inches (17.8 cm) should not be used at all. In most cases it will be too runny to set properly, and may lack a lot of the strength and durability people generally expect.
At-Home Testing Alternatives
A mold and measuring rod are the standard means through which slump is measured, but it these tools aren’t necessarily required, particularly if only an estimate is really needed. Homeowners or small project craftsmen who are working with smaller amounts of concrete can perform a slump test without purchasing special equipment by removing the bottom from a paper cup and inverting it on a level surface. The form should be filled with concrete, tamped it down gently, and the top leveled off. Testers can then remove the cup and measure the height of the concrete, comparing that height to the height of the paper cup to determine the amount of slump.
The slump will naturally be less using this method than it would if a commercial mold was used, but a lot of this is because the overall amounts of concrete are smaller. If the concrete slumps to about 75% of the cup’s height, it is usually a good consistency for pouring. This is not as accurate as a test using a standard mold, but it can be a good general guide.