A rod mill is an ore grinding mechanism that uses a number of loose steel rods within a rotating drum to provide its attrition or grinding action. An ore charge is added to the drum, and as it rotates, friction between the tumbling rods breaks the ore down into finer particles. Although similar in operation, a rod mill is often more effective than a ball mill as it requires lower rotational speeds and less steel to achieve the same results. It is, however, limited to maximum rod and drum lengths of approximately 20 feet (6 meters) and is generally only used for wet grinding processes. The rod mill also tends to suffer from accelerated drum liner and lifter wear due to the increased weight of the rods.
Mills of various types have been used for centuries to break solids or coarse particulate materials down into finer finished products. From the humble mortar and pestle through animal, wind, and water driven mills to the giant electrically driven versions common in modern industrial applications, all share one common characteristic: mechanical attrition or grinding. All mill types utilize a grinding process of one or another description to gradually reduce the size of the initial charge of material. In older mills, for example, this action was achieved by placing the coarse material between two mill stones and turning one against the other to produce a finer end product.
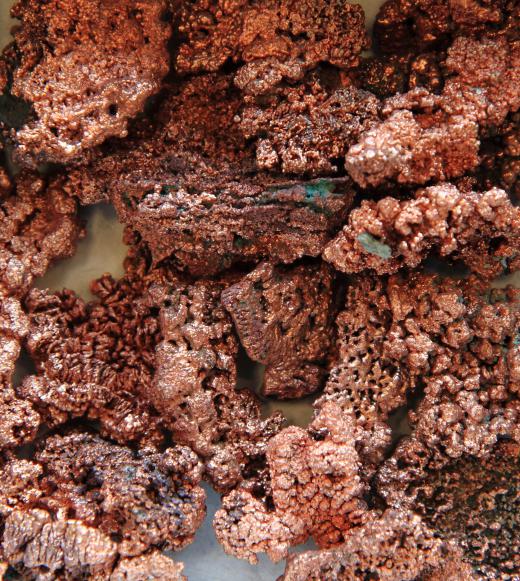
Modern rotary mills make apply the same principle by tumbling loose grinding elements around in a closed drum to which the charge material is added. Common examples are rod and ball mills, both of which are of the rotary drum type which rely on internal grinding agents to achieve their milling action. Unlike the ball mill which utilizes a large number of hardened steel balls to impart the grinding action, the rod mill uses steel rods lying within the drum and parallel to its axis. When the drum rotates, these rods roll around inside it, thereby crushing the feed material between them.
The rod mill is generally more efficient than the ball mill due to its more effective cascading action and the greater bearing surface offered by the rods. This means it can operate at lower speeds and with less grinding agents and producing less undesirable slimes byproduct. Rod mills do, however, require more attention during operation to prevent rod tangles and are generally ineffective at dry milling operations. They are also limited to a maximum rod length of approximately 20 feet (6 meters) which means they are generally smaller than ball mills. Rod mills also exhibit more liner and lifter wear than other mill types due to the comparatively high weights of the rods.