A press brake is a piece of heavy-duty industrial equipment used to bend and shape metal. These machines may be found in sheet metal fabrication shops, metalworking facilities and duct work manufacturing shops. Using a press brake, workers can bend metal sheets or plates to form duct work, tools and consumer goods. The press brake is a very large and complex machine, and generally requires extensive training before workers can safely operate the unit.
Several types of press brakes are available, though each relies on the same basic operating components. A ram, or press, directs force down onto the metal. Using a die, or mold, workers can control the ram and determine the angle and profile of the metal bending process.
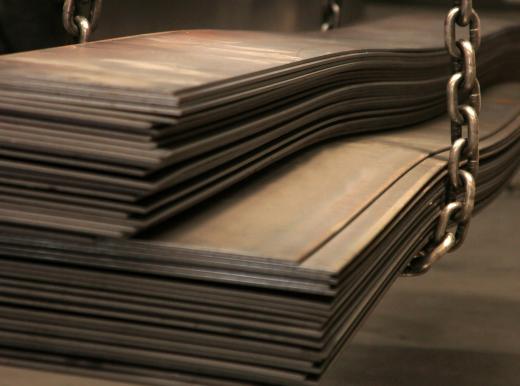
Traditional press brakes relied on a mechanical operating system. An internal motor caused a flywheel to spin, which drove the ram up and down to bend the metal. More advanced pneumatic press brakes use air pressure to increase the speed and force of the ram. Modern hydraulic model include hydraulic fluid in a large cylinder, resulting in the most consistent speed and force.
Rather than place the metal on a flat surface, workers insert specialty dies below the ram to form the metal into the desired shape. A V-block die, for example, will cause the metal to form a V-shape as the ram descends. Other types of dies can be used to create curves and channels, as well as any number of angles.
The most advanced press brake models now include a backgauge feature, which allows users to make more complex cuts relatively quickly. The backgauge repositions the metal after each bend to form more complex bends or shapes. This means workers do not have to remove and replace the metal from the machine after each step.
Compared to manual bending techniques, the press brake minimizes errors and related waste during metalworking. This machine also speeds up production, which can save companies money in labor costs. Finally, a press brake can bend and shape metal with a great deal more force than manual methods, resulting in more advanced metalworking creations.
Special software can even be added to a press brake to allow for rapid production with little human input or oversight. Workers transfer project information into a computer program, which then controls the press brake to complete the required bends. Companies can also save these programs to save time on projects that are frequently repeated.