A pocket screw jig is a device used by woodworkers to drill pocket holes, a technique used to strengthen butt joints, which are frequently used in cabinetry and other woodworking applications. Some woodworkers design and build their own jigs, but the quality and cost-efficiency of those available on the market are good enough to justify most woodworkers buying them. When used properly, a pocket screw jig will dramatically reduce the amount of time spent in creating pocket screw holes. The earliest use of pocket screws is believed to have been in ancient Egypt, where two pieces of wood would be clamped together and a hole drilled from the outside piece into the inside piece. A glued-up dowel was then inserted into the hole and cut off flush with the surface.
A butt joint is created when two pieces of wood are joined surface-to-surface. When secured only with glue, they’re very weak, especially when one of the glued surfaces is end-grain, which is difficult to glue securely. There are a number of ways to strengthen a butt joint, including mortise-and-tenon connections, dowels, biscuits, and pocket screw holes. For many joints, carpenters will prefer one of the other methods, but when many butt joints must be made, as in making cabinet carcasses or face frames, an easy and efficient solution is to use a pocket screw jig to make pocket screw holes.
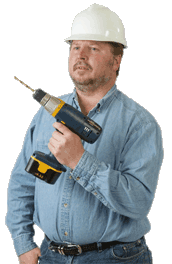
Pocket screw holes are usually drilled in pairs for enhanced strength, near the end of the workpiece being butted up against the other. The holes are generally drilled from the back side of the workpiece, so that they won’t show on the finished piece. The pocket holes must be drilled at a very sharp angle to the surface, toward the end, so that the screws will come out of the end of the workpiece. Once the holes are drilled, self-tapping screws are inserted and used to join the two pieces together. If done without a jig, the cabinetmaker must measure carefully and attempt to drill the hole freehand; most freehand pocket screw holes will have problems, the most common of which is that the hole will exit the other face of the workpiece rather than the end.
A commercially purchased pocket screw jig is made of metal and when configured properly and clamped to the workpiece, lines up paired guides for drill bits to drill the holes neatly and accurately. It can be configured to accommodate different size workpieces and screw lengths so that the screws will have maximum gripping power. Special stepped drill bits are used, and care is taken to control the depth of the drilling, usually with collars secured with a set screw. A commercially purchased pocket screw jig will also have comprehensive instructions for the woodworker.
Many dedicated woodworkers prefer to make as many of their jigs as they can, eschewing store-bought products for shop-made equipment. Making a pocket screw jig in one’s own shop can be a very rewarding project which has been undertaken by many woodworkers. There are many approaches, some of which use a drill to make the holes, and the jig itself is portable, moving from spot to spot on the workpiece. Other approaches call for a router to be the cutting tool, making a swept cut into the workpiece, following which the screw hole is easily drilled. Plans for shop-made pocket screw jigs can easily be acquired from other woodworkers online, and give the home-shop woodworker the added advantage of being able to modify them however desired.