A pneumatic hammer is a member of a family of power tools that use compressed air to drive a cyclic percussion mechanism. In turn the repeated percussion force of this mechanism is transferred to a drill or chisel tool bit. The pneumatic hammer is used to drill into, break up, or chip tough materials such as concrete, asphalt, or tiles. Air powered hammers are typically large tools used in heavy construction, mining, and geological exploration; smaller types are sometimes found in the handyman's tool kit.
Impact driven tools such as chisels and rock boring drills have been in use for centuries and were powered by sweat, muscle, and sledgehammers prior to the introduction of pneumatics. More commonly referred to as a jackhammer, the pneumatic hammer revolutionized the construction and mining industries with its single operator use and high speeds. As related technologies advanced, the jackhammer became more reliable, quieter, and smaller, thus effectively extending the tool's potential uses to include light industrial, domestic, and hobby applications. Today the pneumatic hammer is commonly used for jobs ranging from shot hole drilling in hard rock mining to chipping tiles in the home.
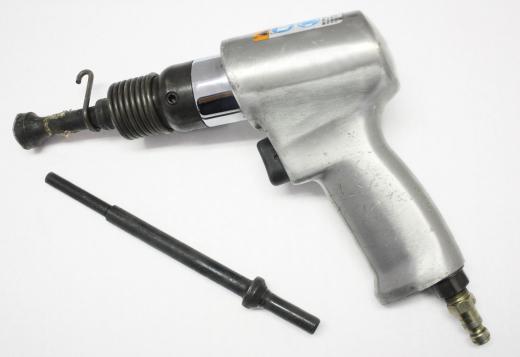
The pneumatic hammer mechanism is a fairly simple reciprocating arrangement driven by compressed air. The percussive force is supplied by a piston driven backward and forwards by the compressed air. The piston is equipped with a percussion head which impacts a similar head on the chisel or drill bit socket on each forward stroke. This impact drives the tool socket and tool bit forward to strike the workpiece. A powerful spring then returns the tool socket to its original position and ready for the next stroke.
This rapidly repeated hammering action of the tool bit is capable of breaking up or drilling into solid concrete and makes short work of softer materials. A wide range of tool bits such as pointed, spade tip, scrabbler, and stake driver bits may be used depending on the particular application. Pneumatic hammer mechanisms are simple, reliable, and require little maintenance. Most are equipped with internal lubrication systems driven by the percussion cycle. As long as the lubrication is being supplied, there is little to go wrong with these rugged tools.
Jackhammer operators, however, are not quite as robust; personal protective equipment (PPE) such as gloves, respirators, and eye and ear protection should be used at all times. These tools generate considerable amounts of fine dust and flying fragments when working on hard materials such as concrete. They are also not the quietest of equipment and also transfer extreme vibrational forces through their handles. The use of PPE is essential to protect against potential hearing loss, eye damage, carpal tunnel syndrome, and circulatory failure in the hands.