A pneumatic controller is a device used to regulate air pressure among several work stations in a manufacturing facility. Attached to a main air line leading from an air compressor, the pneumatic controller allows the operator to adjust the controller and vary the air pressure while allowing the main air pressure to remain at a high operational level. The benefits of adjusting the air pressure via a pneumatic controller are that condensation from the compressor running at variable speeds is eliminated, thereby reducing the amount of water in the air system.
By operating air-powered tools and machinery in a manufacturing setting, the process of manufacturing is made much faster. This results in increased production as well as increased profits. Most of the air-powered machines require different air pressures to operate properly; this is why the pneumatic controller is a valued asset to the system. Acting much like an electrical circuit board, the pneumatic controller is able to adjust and divide the air supply. Once adjusted, the air is directed in the proper pressure to the individual components of the work place.
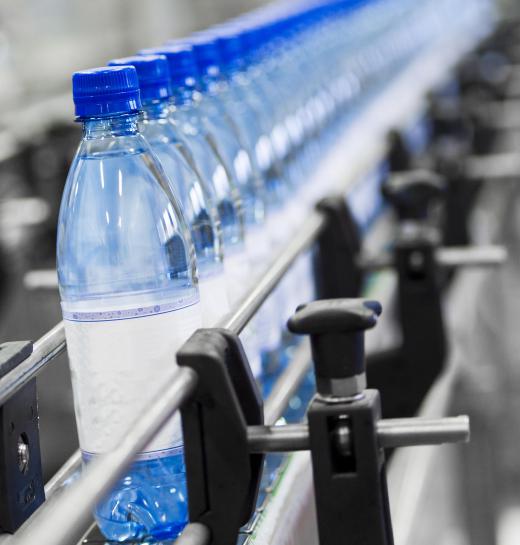
Most manufacturing plants use a pneumatic controller on the main air lines; some use a separate pneumatic controller at each work station, however. This arrangement allows an individual operator to make precise adjustments to each tool in order to produce the best results possible at each work station. Often the individual pneumatic controller also allows maintenance to be provided to individual work stations without halting production on the entire line.
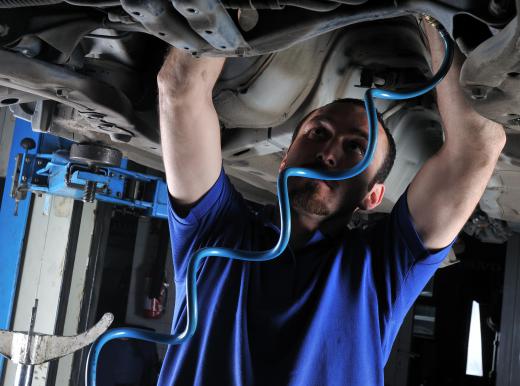
Air-powered equipment and tools are prone to rust and damage from water that occurs within the air system. Many pneumatic controller designs allow for automatic oiling devices to be installed upstream from the tool. These oilers provide a slow but steady drip of oil into the air line. By introducing oil into the air line, rust and damage is eliminated and there is less downtime due to changing out faulty tools.
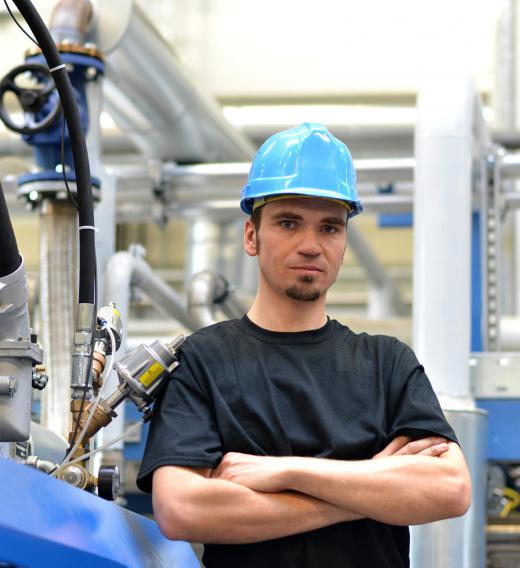
Controllers are often installed directly behind an air compressor. This installation allows multiple compressors to be operated on intervals, which allow the compressors to be maintained while switching between them without hindering production. As the controller is switched from one compressor to another, one can then be shut down and serviced while the other maintains air production to the plant. With this type of system, an entire compressing unit can be removed and replaced without giving up any production time.