Phosphate coating is a type of treatment for metals, especially iron and steel, in which a layer of a phosphate of another metal, such as zinc, is applied to provide protection against corrosion. Phosphate coating a steel part provides an inert layer that will help prevent rusting as well as provide a stable base for application of other coatings such as paint. Phosphates are dissolved in an acidic solution and when the metal part is submerged in the phosphate acid bath, a chemical reaction results that causes the phosphate to be deposited on the surface.
A Phosphoric acid solution is used as the base for the phosphate coating bath. The desired phosphate for the coating is dissolved in the solution. When the piece to be coated is submerged in the solution, the acid reacts with the metal. This causes the pH of the solution immediately around the metal piece to rise which results in the phosphate being precipitated from the solution and onto the metal. The phosphate binds to the metal in a layer of fairly even thickness regardless of part's shape.
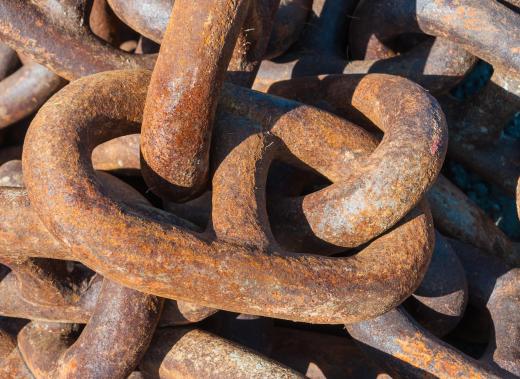
The primary metals used in phosphate coatings are zinc, manganese, and iron. Zinc and manganese phosphates provide a stronger corrosion resistance than iron phosphate, but as a phosphate layer is somewhat porous, none of the three phosphates is a perfect barrier to rust or other corrosion. The phosphate coating instead provides a base for further coatings or treatments.
Oil is often applied to a phosphate coating as further protection against corrosion. This works well for preventing rust because the porous phosphate coating absorbs the oil, and together, the two create an effective barrier. This type of coating is often known as a P&O coating, for phosphate and oil. Other coatings are often applied over phosphate coatings, especially sealers and lubricants. These type of treatments are effective in preventing corrosion and reducing wear on moving parts by reducing friction.
Metal parts that are to be painted are often phosphate coated in preparation for the paint application. In these cases, corrosion resistance is secondary to the characteristics of the coating, which makes it particularly useful as an underlying layer for the paint to adhere to. The porous phosphate coating absorbs and binds to the paint much more effectively than it would to bare metal.