A melting furnace is an appliance capable of heating materials to such a high temperature that they melt, which from a chemical perspective basically means that they reach the critical threshold temperature at which they convert from a solid to a liquid. Not all materials will melt, and those that do often have different melting points. As such, most furnaces are intended for handling certain types of jobs. Most are adjustable which allows for some flexibility and internal control. There can be a wide variety in terms of furnace size and capabilities, with some intended for more or less personal use, as in a private shop or garage, whereas as others are much larger and are used industrially. Still, all usually fall within one of four major types or formats: cupola furnaces, electric arc furnaces, induction furnaces, and crucible furnaces. Each has a slightly different style and use profile, but the overarching goal is usually the same no matter the specifics.
Understanding the Basics
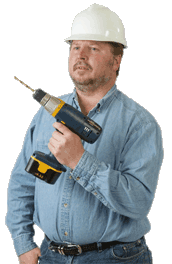
Metals are far and away the most common material that people melt down in furnaces. Melted or liquefied metal is much more malleable, and can be formed, molded, and reconfigured with relative ease. This applies both to things like stainless steel and aluminum as well as precious metals like gold and silver. Melting makes it possible to shape and repurpose these raw elements into something useful, and a furnace is usually the most controlled and efficient way to proceed.
The furnace is a tool that has been used by people for a very long time. The earliest furnace is believed to have originated with the Indus Valley Civilization of the Indian subcontinent, and has been dated to somewhere between 2500 and 1800 BC. The melting furnace is an industrial version of this concept, and is typically used for the production of specific materials or as a heat source.
Cupola Models
Some industrial scholars consider the cupola furnace to be the most historically popular form of melting furnace for ferrous, or iron-based, materials. The device is at its core a vertical shaft that resembles a smoke stack. The inside is usually lined with refractory bricks. The most primitive models are little more than basic enclosed towers, usually with a system of shelves and trays for catching the product. More modern examples have temperature controls and a more formalized melt-and-catch system. Air blowing nozzles, used to increase heat, can also be found inside the shaft in many cases. The cupola furnace can be used for various tasks, such as producing liquid ore and melting cast iron or bronzes.
Electric Arcs
Electric arc furnaces are also very popular for re-melting steel scrap. Smaller units are sometimes used for producing cast-iron products, too. As the name implies, this model uses an electric arc to generate heat. The arc creates an electrical breakdown of gas that causes what’s known as “plasma discharge,” which leads to more rapid melting. Inside the furnace unit, material is put in direct contact with the arc which, in some units, can reach temperatures of up to 3275° Fahrenheit (1800° Celsius). A lot depends on the size of the furnace and what exactly is being melted.
Induction Method
The induction furnace is generally used for melting both ferrous and non-ferrous alloys. It usually employs a water-cooled copper helical coil into which a crucible is installed. When alternating current passes through the coil, the crucible is heated. This model is generally praised for its energy efficiency and the lack of pollution it causes. Induction furnaces tend to be a lot more contained and as a result tend to make less of a mess, as well. Most iron foundries now use the induction furnace instead of the cupola furnace because of these advantages; it is also popular in a number of industrial settings where efficiency and cleanliness are concerns.
Crucible Furnaces
The crucible furnace is considered to be the oldest type of melting furnace, and also the most primitive. It is still used in many more traditional settings and is common for a number of small projects, but tends to be less popular in industry. Its basic design consists of a refractory crucible into which the material to be heated is placed. The material is then heated from outside the crucible wall. Gas-fired versions of this often use a burner to generate heat, while electric models use heating elements.