A gear shaper is a machine that cuts teeth on external or internal helical and spur gears with a cutting bit equipped with teeth of the same pitch and shape as those of the completed gear. The bit reciprocates vertically in relation to the gear blank, thereby cutting some material away on each down stroke. Once the downstroke is complete, the bit moves away from the blank and lifts for the next stroke. Once at the top of the upstroke, the bit moves back into position and moves down to make another cut. During this process, the blank is rotated to facilitate the cutting of teeth around its entire circumference.
There are several different engineering processes that go into making spur and helical gears, sprockets, and geared racks. The gear shaper is one of the more common of these machining processes and can cut both external and internal gears of all sizes. Unlike rotary processes such as hobbing, a gear shaper uses a cutting bit which follows a reciprocating vertical path to cut the gear teeth. The cutting bit is equipped with tooth-like cutting edges of the same pitch and shape as those of the completed gear and travels vertically on a reciprocating ram. The gear blank rotates around its own axis in the machine but does not move positionally during cutting.
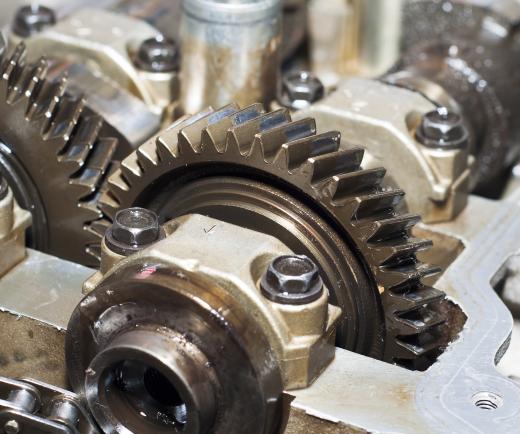
During cutting operations, the gear shaper positions the blank gear stock and the cutting bit on parallel axis to each other in the same way as completed, meshing gears. The cutting cycle begins with the bit's downward stroke against the face of the blank gear's circumference with the resultant removal of a nominal amount of material. At the bottom of the stroke, the bit is moved a short distance away from the gear blank and lifted to the top of the stroke. There it moves back into the cutting position and lowers again to make the next cut. During this process the gear blank rotates to advance the position of the cut.
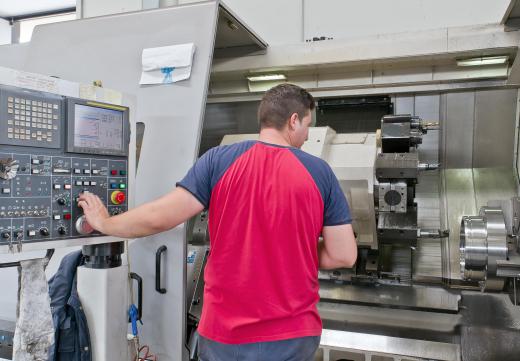
This process is repeated continuously until the entire gear circumference has been cut. During cutting, the bit is also advanced towards the gear blank, thereby progressively deepening the cuts until the gear is completed. During cutting, a constant stream of oil is directed onto the cut point which lubricates the bit and eases the cutting and removing swarf or metal chips. Very large gears are typically gashed or rough cut prior to final finishing on the gear shaper to speed up production. Most gear shapers are driven by computer numerical control (CNC) systems which provide extremely accurate and precise control of the cutting process.