A fillet weld is the most common type of weld, and it is used to join two pieces of flat steel at a 90° angle. It is produced by running a weld bead at a 45° angle to a 90° corner; it resembles a triangle when viewed from the side. The weld is used to fill the area where two pieces of steel meet, giving it its name.
Used to make lap, corner and "T" joints, the fillet weld is the most basic of welds. The depth of the penetration, as in all welds, determines its strength. It is important, when creating this type of weld, that the welding rod travel the same distance up both sides of the joint. Failure to get sufficient penetration on both pieces of the joint will result in a weld that has far less strength than one that has equal distribution on both sides.
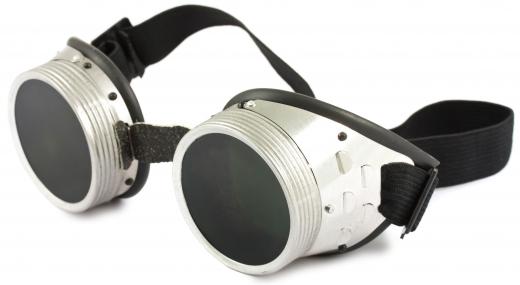
A proper fillet weld requires a greater heat setting than a comparable butt weld. The trick in learning to create a proper fillet is in learning to properly gauge the amount of weld deposited into the joint. A joint with too little weld will have a dish-like appearance to the weld bead, which often occurs if the welder is moving too fast. Conversely, a weld that is made by going too slow will have a bubble appearance or appear piled into the joint. The proper weld should have a flat appearance when viewed from the side.
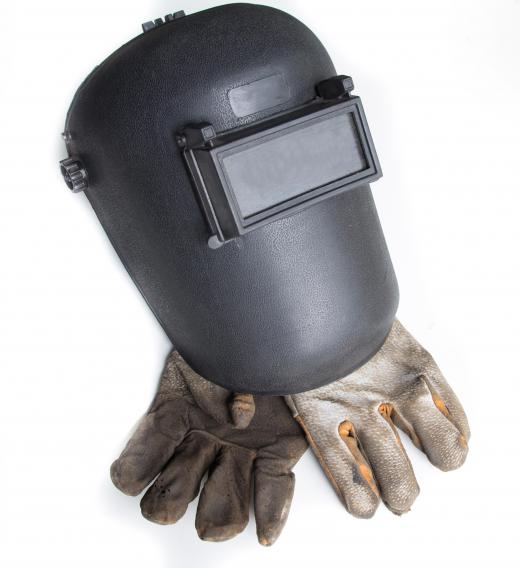
When a welder uses a fillet to weld a lap joint, it is important that the top corner of the joint not be melted away. This requires that the weld be placed below the top edge and that the amount of heat and penetration not be allowed to travel up to the edge of the top piece of steel. Careful technique by the welder must be practiced to avoid over-penetration by moving the weld puddle too slowly. Speed and heat settings are key to doing this correctly.
While the fillet is estimated to fill 80% of all welds, it still requires training and practice to be correctly applied every time. It requires such attention simply because it is used predominately on every job site. Applied properly, the fillet is the workhorse of all welds.