A double check valve is a plumbing fitting that prevents back siphonage to protect fresh water supplies from contamination. This fitting is typically installed on fresh water supplies for garden irrigation, combi-boiler, and fire suppression feeds where a backflow contamination risk exists. The unit consists of two standard backflow check valves mounted in series in a single housing. The basic concepts behind these valves include redundancy and the more reliable seating of each valve. Larger industrial type double check valves often include an isolation valve on either end and test cocks at various points while residential examples are typically sleek, in-line designs.
Back siphonage or backflow is a major source of fresh water contamination and has been positively linked with many waterborne disease outbreaks. Backflow contamination risks exist wherever fresh drinking water supplies are used to feed fire sprinkler systems, garden or agricultural irrigation, chemical dosing installations, or combination boilers. If no backflow protection is fitted to these setups, any significant drop in fresh side pressure will see contaminated water siphoning back into the potable supply. The best way of protecting fresh water supplies against this backflow is the installation of a backflow prevention device such as a double check valve.
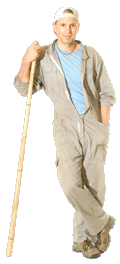
A check valve is a fairly simple, robust, and reliable one-way valve that relies on a spring or gravity loaded plunger or a diaphragm to allow fluids to flow in one direction only. This is typically achieved by constructing the valve in such a way that the valve disc opens when exposed to pressure from one side and is forced closed positively should that pressure drop or be reversed. The double check valve features two such units mounted in series with the water flow path. The concept behind this design is a two-fold combination of redundancy and efficiency.
The redundancy benefits of the double check valve are pretty self explanatory; one valve is always being able to back the other up in the case of a blockage or mechanism failure. From an efficiency perspective, the pressure differential across the two valves during operation means that both are able to seat more effectively, thus boosting the overall efficacy of the system. The flexibility of the double check valve is further enhanced by the inclusion of dual shutoff valves on either end of the fitting which allow either side of the circuit to be isolated should the need arise. These and smaller test cocks used to test the functioning of the system are generally found on larger industrial variants. Domestic double check valves are generally smaller and more simple and are typically in-line designs or are incorporated into standard faucets or bibs.