A countersink is a cone-like hole cut into an object, so that the head of a screw, bolt or nail is flush to the surface. The tool used to cut countersinks also is referred to as a countersink, and it comes in many styles. Countersinks are very similar to counterbores, where a shallow, round hole is drilled on top of a smaller bore to fit the head of a bolt. Countersinking can be a very beneficial procedure, because it removes any sharp edges caused by screw, bolt or nail heads protruding from the surface of an object.
The chamfer angles of a countersink can vary, depending on the tool being used or the chamfer angle of the screw or bolt. Typically, chamfer angles are either 60, 82, 90, 100, 110 or 120 degrees, with the angle being measured from either end of the bore opening. Countersinks typically are conical, which is referred to as a plunging application. Some countersinks have beveled edges to allow for the intersection of two different planes.
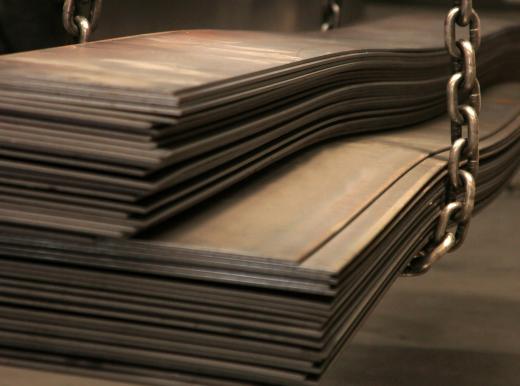
Another type of countersinking method is known as form countersinking, which is used exclusively in sheet metal applications. This type of countersink effectively increases strength, because multiple countersinks are brought together. The two methods for producing such countersinks are known as modified radius dimpling and coin dimpling.
Performing a countersinking operation requires a special countersinking tool. Countersink drill bits come in a wide variety of sizes and angles to accommodate nearly any screw or bolt head, and they typically are used on milling machines. These bits, however, are not exclusive to the mill; countersink bits also can be used on drills, drill presses and lathes.
One type of countersinking tool is known as a cross-hole countersink cutter. This is a conical device with a hole on one side of the cone itself. This hole is a very important part of the tool, because it not only creates a cutting edge, it also provides an area for exhausted materials — such as sawdust and metal chips — to be collected. This tool is not completely symmetrical, which prevents the entire cone from rubbing against the chamfer, so that the hole can be used as a cutting edge.
The cross-hole cutter, however, is not used for most cutting applications. Instead, it is used for finishing work where a sharp tool is not necessary. When countersinks are actually cut, a fluted countersink cutter is the tool that is employed. This tool is somewhat similar to an end mill for a milling machine, but it is in the shape of a cone. The cone itself comes in a variety of angles, which typically are the six common angles — 60, 82, 90, 100, 110 or 120 degrees.
Another type of tool is the back countersink, which is often used for accessing hard-to-reach places. This consists of two components: a rod and the bit itself. The rod is positioned into place where the countersinking procedure is to take place, and then the bit itself is added onto the rod.