Blast furnaces are devices that are used in the process of iron smelting. The heat created in the furnace makes it possible to produce the iron from iron oxide ores. A blast of air contained within the blast furnace itself helps to intensify the degree of heat, expediting the smelting process.
In appearance, the typical blast furnace is in the form of a tower. Secure doors are mounted onto the front of the device, making it possible to feed the raw materials into the furnace either by hand or with the use of a conveyor belt. Some furnaces of this type are also equipped with a drawer at the base that makes the collection of slag and other finished products much easier.
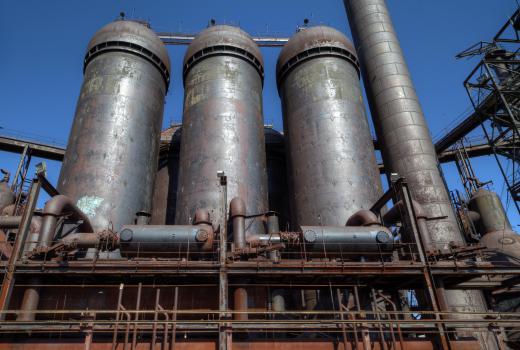
Furnaces of this type are often used in the steelmaking process. A blast furnace is ideal for combining charcoal and iron ore together. The extreme heat in this type of furnace makes it possible to melt both substances into an integrated liquid metal that ultimately forms what is known as pig iron. The pig iron is removed from the base of the furnace from time to time, and used in the creation of a number of different types of building materials.
Along with charcoal and iron ore, limestone or some other type of flux can also be introduced into the mixture. The tower design of the furnace makes it very easy to control the degree of heat generated in the main chamber, thus allowing the operator to temper the raw materials as needed. While many aspects of ironworking have benefited from modern technology, the basic design and operation of the blast furnace has remained virtually unchanged for centuries, owing to the fact that it is still the most economic way to produce iron on large scale.
The origin of the blast furnace is usually traced back to Chine during the fifth century BCE. By the Middle Ages, the use of this type of furnace was found in England as well as parts of Europe. The present day design of the device is often attributed to various innovators of the early 18th century, who refined the ability of the blast furnace to produce larger amounts of product in a single session. At the same time, this newer design also make it possible to make use of the blast furnace gas produced by the release of carbon monoxide from the charcoal as a reducing agent for the pig iron created in the furnace.
Furnaces of this type remain an important part of the steelmaking process around the world. Relatively inexpensive to operate and maintain, a blast furnace can last for generations before it must be replaced. The economic aspect of the furnace helps to ensure that steel makers are able to remain competitive in today’s world, even when metals produced by other methods become difficult to sell.
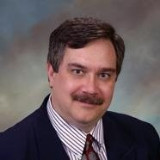