Urethane can be used for many industrial purposes as well as in residential settings. An alternative to plastic, rubber, or metal, it can often withstand strong impacts, hold its shape after being manipulated, and resist many different chemicals. Heat tolerance is typically another beneficial quality. Different types of urethane sheet can be distinguished by their size, thickness, color, as well as hardness, also called durometer. The sheets can be manufactured by extrusion or thermosetting and product variations sometimes include metal-backed, no wax, or dual-layer urethane products.
The process used to manufacture a urethane sheet generally affects its ultimate quality. Final products usually begin as a liquid polyurethane polymer, which can be mixed with other compounds according to product guidelines. Once solidified, it is typically heated, extruded through machinery, and rolled into a flat sheet. Extrusion is a process often used to manufacture this durable product.
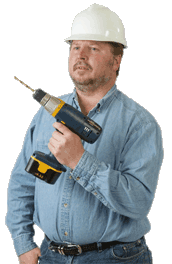
Heat and energy are generally used to produce a urethane sheet by thermosetting. The molecules of the sheet are altered chemically into a three-dimensional structure that has a higher melting point than the initial material. Surface durability in extreme environments is typically one characteristic of thermoset urethane sheets, as well as the ability to block sound when installed in a home.
While one type of urethane sheet can be used as soundproofing in the walls of a house, another has enough abrasion resistance to be used in industrial manufacturing. Some sheets can be used for conveyor belts or material handling equipment. Various pads and other liners used in vehicles and aircraft, mining, and steel service applications are made of urethane. Sheet-type urethane products are sometimes made into films as well as adhesives that can be custom sized for each application.
A urethane sheet can be supported by a metal backing. This configuration typically enables the sheet to be shaped as needed. There are also varieties backed by a fabric that can enable installers to glue the sheet to another surface. Manufacturing processes are sometimes simplified by eliminating stages in which wax or mold release compounds are added. Some manufacturers can provide a urethane sheet with one side wax-free or both sides without wax.
In some cases, a urethane sheet can consist of two layers bonded together. This product generally tolerates harsher conditions than a single-layer sheet. No matter what type of urethane sheet is chosen, various colors, sizes, and thicknesses are often available depending on the process or environment it is used in.
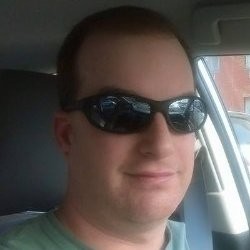