There are a number of different types of pallet systems, some of which are better than others for different situations, but in general they can all be broken down into five main categories. Selective pallet racking is usually the most common in large warehouses, though drive-in systems that can easily accommodate forklifts and loading trucks are frequently used, as well. Flow and push-back designs both make use of depth to increase storage capacity and are particularly popular when space is at a premium. The so-called inventory methods are usually organized based on demand, either perceived or realized, and this demand is what determines where things are placed and how easy they are to access. All systems offer a means of storing large quantities of materials and goods in a more compact space, though most require the use of a forklift or pallet jack to place palletized materials on storage racks.
Choosing and Differentiating
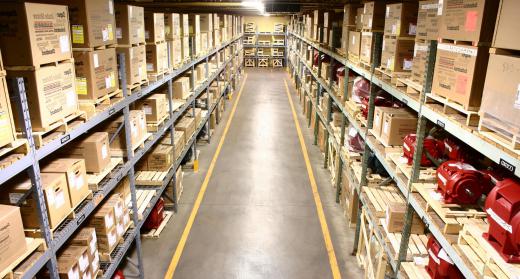
All five types are widely used in warehouses, retail facilities, manufacturing plants, and distribution centers. In most cases, stock managers choose a system based on two main factors: frequency of use and ease of accessibility. Different methods work better in different places. A lot has to do with what’s in the pallets, how often they need to be moved, and how far they’re going.
Selective Pallet Racking
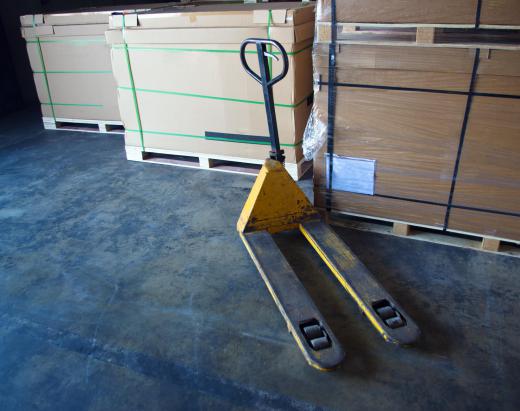
In general, a system known as “selective racking” is the most common, particularly for major distribution warehouses and spaces where there is a high volume of material to be stored and moved. It typically provides pallet storage one unit deep in up to 50 standard frames for easy access at all times, and is available in two configurations. The roll form, also known as the “clip-in style,” contains teardrop-shaped clips that can be easily moved for shelf height adjustment. This can be advantageous in cases where the size of the load varies. Structural rack systems feature horizontal load beams attached directly to the uprights for greater load-bearing capacity. Very narrow aisle (VNA) is an alternative selective system designed with a tighter arrangement to further maximize storage space.
Drive-In Systems
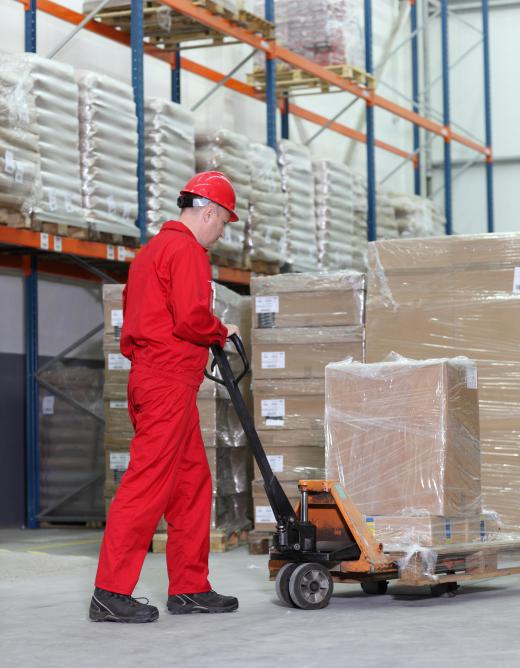
Drive-in or drive-through systems provide pallet storage in stacked rows wide enough for a forklift. In terms of distinction, if a stacked row has an entry point at only one end, it’s usually considered to be a drive-in system. An entry point at both ends of the stacked rows makes it a drive-through system.
Flow and Push-Back Designs
Pallet flow systems make use of depth to increase storage capacity. These high-density pallet systems typically use a slightly slanted rail with rollers, which enables pallets to easily glide along. Pallet flow systems most often require an intricate mechanized system to set the speed of moving pallets, but are often a good choice when there’s a lot of movement that happens on an almost constant basis.
Push-back pallet systems also make use of depth. Under this sort of scenario, each stacked row or bay can be up to six pallets deep. Each pallet is stored on carts with wheels that fit on a specially designed rail that uses gravity to transport heavy pallets.
Inventory Methods
There are two related inventory-based storage methods. In a first-in, first-out (FIFO) system, pallets are filled from one end of the storage rack, which effectively shoves the goods they’re made of to the opposite end. Those goods then lead the row on the other side and will, at least in theory, be the first ones removed from the opposite end. This inventory method is helpful when goods have expiration dates or if shelf life becomes an issue. Drive-through and pallet flow systems are often FIFO systems.
In a last-in, first-out (LIFO) system, pallets are loaded and unloaded from the same side. This provides continuity in ordering and unloading, and is usually most efficient in cases where expiration dates are not a concern Push-back pallet and drive-in systems are almost always LIFO systems.