Process control methods represent ways a company can inspect and adjust production methods in order to manufacture quality products. In some cases, these methods are the only way a company can discover goods or services that fail to meet internal standards. A few different process control methods include check sheets, control charts, and statistics reports. These are just a few of many different manufacturing control methods a company may implement in one or more production departments. Companies must select those methods that work best for the good produced, department, and time allotted for conducting checks.
Check sheets are physical process control methods that use both on-site reviews and paperwork to create a historical control record. Here, a supervisor or other employee must visit the production department in which check sheets are located and used for quality control. An inspection is typically necessary to review and look at the goods produced. Answering question on the check sheet or filling out short sections or statements is the norm here. The result is a check sheet that describes the quality of the goods and overall process.

Control charts are both similar and different to check sheets; the biggest difference is that a specific standard exists that produced goods must meet. For example, the control chart may have a lower limit and upper limit goods must fall between, with a middle limit that represents the expected standard. Process control methods using control charts may work best for testing a batch of goods. For example, testing a select sample of goods to ensure they each fall within the lower and upper limit generally means the entire batch should meet the company’s internal standards. Tested products that fall outside of the control limits may indicate flaws in the production process that need adjusting.
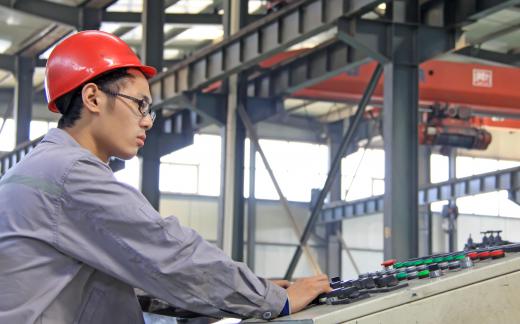
Statistical process control methods are much more involved than the other two control methods here. Companies need to create statistical models — such as a probability chart that defines the success or failure of goods — in which to test both produced goods and departments. Any tests that result in outputs outside of the desired or expected failure rate are unacceptable. For example, a company may accept a failure rate of three percent out of 1,000 goods produced; any differences here are unacceptable and need further research. Another type of statistic may be a deviation from acceptable standards; goods that are too far from the accepted material will not usually pass the inspection process.