The best tips for total quality management (TQM) in manufacturing are to involve everyone in the organization in the pursuit of quality control, and to foster a corporate culture of personal ownership among staff. Teaching staff to understand that it is typically systems and not individuals that cause a degradation in quality, is a crucial component as well. Training employees to think proactively while on the job, instead of passively waiting for directions, also tends to increase the overall quality of a manufacturer's goods.
Total quality management — whether applied in manufacturing settings or in service sectors — rests heavily upon the company's staff knowing that a team approach ensures higher quality performance. If someone working within one department of the company does not feel a responsibility to another part of the company, this results in less engagement among staff. When employees do not take pride in their workmanship, production mishaps occur and down time can result. Employees who are involved in total quality management in manufacturing will tend to feel a greater sense of responsibility to the overall operation. This has been shown, in many cases, to increase productivity.
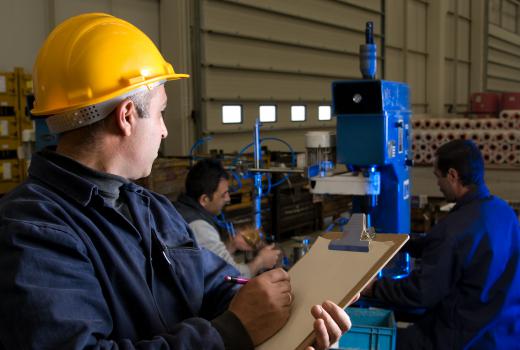
A common misperception in TQM is that individual workers are responsible for failures in quality control. Managers may focus attention on one slow performer, while missing much larger causes for declines in productivity. Often it is organizational systems that produce the larger impact on productivity.
If one worker is lagging in his or her personal productivity, this negatively impacts a company's productivity. If, however, an assembly operation is organized in such a way that causes five workers to each expend 15 extra minutes on average every day in unproductive activities, that will have a much bigger impact on productivity. In lean manufacturing operations, people are often rewarded for pointing out inefficient aspects of the operation.
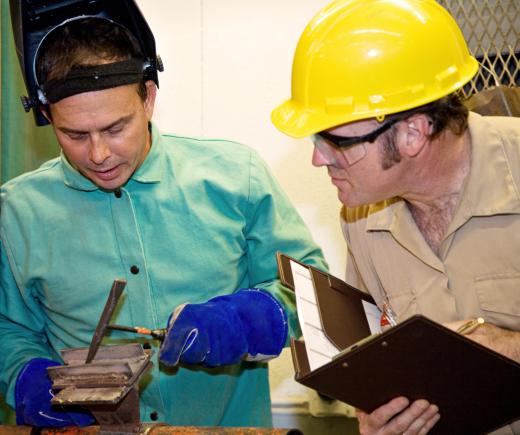
Helping employees make the transition from merely reacting to a problem to proactively remedying or even preventing a problem, is another very important tip for total quality management in manufacturing. When an employee feels a sense of ownership to his or her work responsibilities, generally productivity increases. An engaged employee will tend to take pride in workmanship.

Often, the engaged employee will feel a greater sense of responsibility to speak to management about anything that may be negatively impacting productivity. Such proactive attitudes usually increase a sense of engagement among employees. Those who are actively engaged in the work process are often highly prized contributors to total quality management in manufacturing.