One of the main strategies in producing quality laser cut leather is to consult the instruction manual for the specifications of the laser cutter. Familiarization with the cutter and the accompanying software aids in design creation and contributes to the quality of the finished laser cut product. Experienced leather crafters recommend using the vacuum exhaust system when laser cutting leather as the process typically produces a strong smelling smoke.
The instruction manual that accompanies laser cutting equipment generally provides the steps and settings necessary for cutting or engraving a variety of materials, including leather. For laser cut leather outlines, make sure the software program depicts a transparent image on the graph layout, with no colors or shading. The image must line up properly on the grid or the laser may not cut out the entire image.
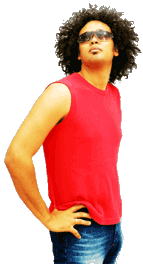
When creating a pattern for a leather design, users should be aware of the width of the cutting beam. If a laser beam cuts a line that is 0.2 millimeters wide, for example, and some lines on the pattern lie closer than 0.5 millimeters apart, the cutter may obliterate both lines simultaneously. Cutting two lines at the same time saves time when positioning one pattern next to another. The width of the cutting beam may also make a difference when designing patterns with intricate cut outs as spaces cut closer than 1 millimeter apart may produce a flimsier latticed pattern than anticipated.
Prior to making laser cut leather, hobbyists must also ensure that the system has the correct combination of speed/power/frequency settings for the amount of wattage being used by the laser cutter. Cutting leather using 30 watts, on some machines, requires a leather cutting setting of 40/90/500. For 75 watts, the setting changes to 60/80/500. Different settings are used for leather engraving. Practicing the cuts and designs on scrap leather before making actual laser cut leather products may spare machine owners from wasting expensive material if the laser does not produce cuts as expected.
The setting for one type of leather material may not be suitable for another. Smoother surfaced leather generally cuts more easily than rougher textured suede. Leather products may also be thinner or thicker than recommended settings, which may not produce the same cutting results. The beam on a laser cutting tool generally cuts material by vaporization, and if the machine is not set correctly for a particular type of material, charring may occur.
Charred lines may appear on laser cut leather if the power setting is too high. Reducing the power and cutting around the design two or three times may produce less charring. Using a paper mask or low-adhesive tape over the leather may also reduce the tendency for charring. Blurred or thickened lines may be the result of smudged mirrors or debris on the rails that animate the cutter or laser table. Performing maintenance on these two areas often improves the appearance of cuts.