There are several advantages of the continuous production of products over production in batches in terms of production volume, cost, energy, and quality. High volume production is possible in a shorter amount of time due to ongoing production and eliminating unnecessary start-up and shutdown steps. Lower unit cost and energy savings can be achieved through automation and reduction of unnecessary labor. Better quality control can also be maintained as there are fewer opportunities for the process to be changed or for human error to impact production.
Continuous production is a method used to maximize the amount of product that is made in a given amount of time and production space. Production generally takes place 24 hours a day, year-round without interruption. With the exception of an unusual outage, equipment is in use at all times and output from the production flow is similarly ongoing.
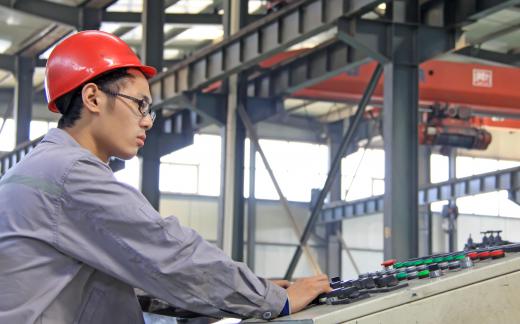
The most obvious advantage of continuous production is the ability to produce high product output in a short amount of time. By running a production line around the clock instead of only during standard work hours, a facility can manufacture more products. This method also avoids wasting time shutting down and restarting equipment on a regular basis that otherwise could be used for production.
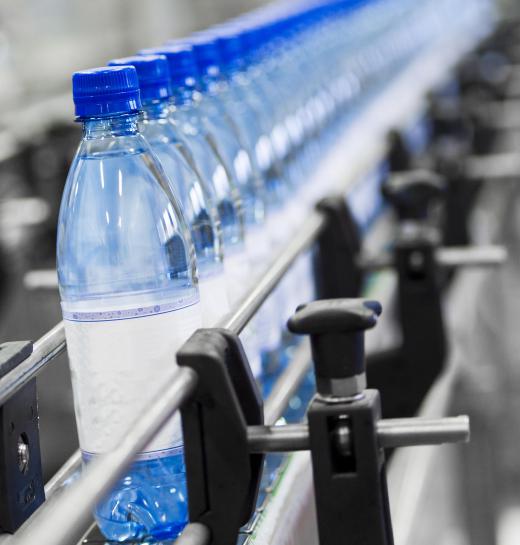
In part due to this compression of the production process in time, continuous production can also lead to low unit cost. This low unit cost is also contributed to in part by cost savings on labor. Less-skilled, less-expensive labor is used for the few tasks that are not automated, while machines do most of the work and perform complex operations. Although the capital cost of equipment can be expensive, high initial cost can be recouped with low unit cost per product from high volume production.
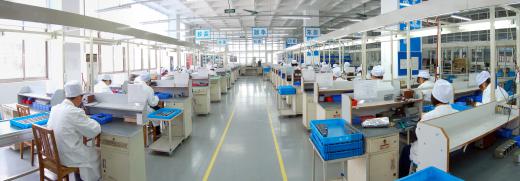
Further savings as well as environmental benefits may result from the energy savings that come from eliminating steps that do not add to the value of the final product. Continuous production can avoid some of the cleaning and sterilization necessary before equipment is allowed to sit idle because the equipment is in constant operation. It also avoids much of the transportation required to move materials to and from storage that would be required with batch production. Rather than sitting in storage until operations begin, material in a continuous production facility is often fed directly into the production line.
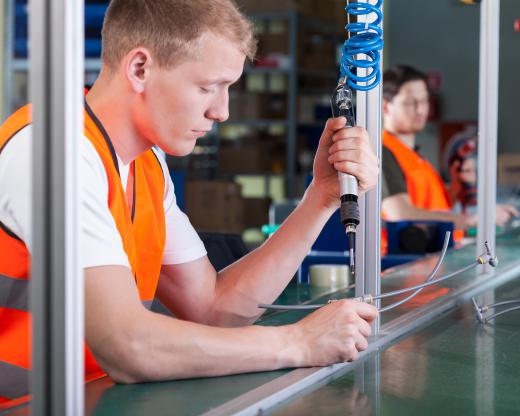
This feature makes this method highly compatible with a common manufacturing strategy referred to as lean manufacturing. Lean manufacturing is based on the premise that any process or product not directly involved with providing value for the customer is waste to be eliminated. Eliminating unnecessary expenditures through continuous production is one measure that may be taken in implementing lean manufacturing.
Another major advantage of this production method is that it can help ensure consistent quality over a high volume of output. The quality of some products, such as food or some chemical products, is highly dependent on consistency in the ingredients and process. By avoiding repeated shutdown and start-up processes, it is much easier to ensure that the process remains unchanged.
Continuous production also contributes to product quality by reducing opportunities for human error. Due to the highly automated nature of the operation, people directly carry out many fewer steps in this type of facility. This minimizes the opportunity for quality to be harmed by errors such as contamination, damage due to improper handling, and so on.