Ejector pins are long pins that are used in the injection molding industry to push the final molded product out of the mold. They are used forcefully to eject the solid part out of the mold and are usually made of high-quality steel. They are also known as knockout pins, knock-out pins or KO pins.
Typically, these pins are extended and retracted to force the part out of the molded cavity and are the cheapest means of ejection. The pins might leave marks behind, so they are usually applied only when the parts have sufficiently cooled down, to avoid the deforming the parts. Ejector pins are available in various sizes and shapes, such as round, bevel-headed, straight and cylindrical. They can be customized and precision-engineered to suit the application. Important factors for one to consider when selecting pins are corrosion resistance, durability, tolerance and tensile strength.
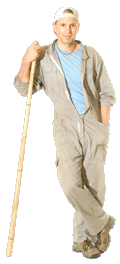
It’s important for the right type of ejector pins to be selected for efficient part production in molding applications. There are three different types of ejector pins available. Each type possesses specific characteristics, and they are used in different environments. The most important factor that differentiates these pins is the temperature at which they can be used, because this affects their durability and life span. Pins made for low temperature environments will deteriorate rapidly when used in a high-temperature setting.
Through hard pins are good all-purpose pins that are heat-treated to be uniformly hard throughout their diameter. They are typically used for plastic injection molding. They are made of steel and can be used in molding environments below 400 degrees Fahrenheit (about 200 degrees Celsius).
Case hardened pins are nitride H13 pins that are suitable for die casting. They can be used at temperatures above 400 degrees Fahrenheit (about 200 degrees Celsius) and are quite durable. They are hard pins that can be drilled or tapped. They chip easily when compare to through hard pins but have a greater life expectancy, even at high temperatures.
Black ejector pins are special pins that were developed for extremely high temperature working environments. They can be used at temperatures from about 1,100-1,800 degrees Fahrenheit (about 600-1,000 degrees Celsius). These pins have a unique protective surface coating that allows them to be used at such extreme temperatures and provides self-lubrication. They are more expensive and are commonly used in automobile injection molding.
Ejector pins can be enhanced by a coating that protects them and makes them more durable. The coating reduces the friction so that the pins survive the wear and tear and the molded part falls out more reliably. It also makes the pins more chemically inert and stable, and it can be applied over treated pins.