Nylon is made through a complex two-step chemical and manufacturing process that first creates the fiber’s strong polymers, then binds them together to create a durable fiber. The term is commonly used to refer to a broad range of polyamides, or synthetic polymers, and encompasses a range of often very different products. Clothing, rope, hard plastic mechanical parts, parachute coverings, and tires are all examples of the synthetic material in action. In most cases the manufacturing process is different for these different items, but the chemical part of their creation tends to be very similar.
Polymerization
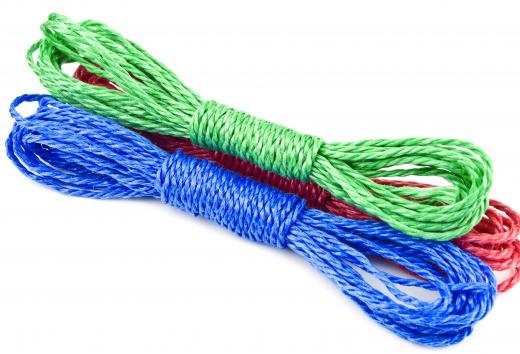
The first thing the manufacturer must do is to combine two sets of molecules. One set has an acid group on each end and the other set has an amine group, made up of basic organic compounds, on each end. There is some room for variation, but using hexamethylene diamine monomers and adipic acid is a common combination. When these two substances are combined, thick crystallized “nylon salts” result. These are commonly known as nylon 6, 6 or simply 6-6. The name is based on the number of carbon atoms between the two acid groups and the two amine groups.
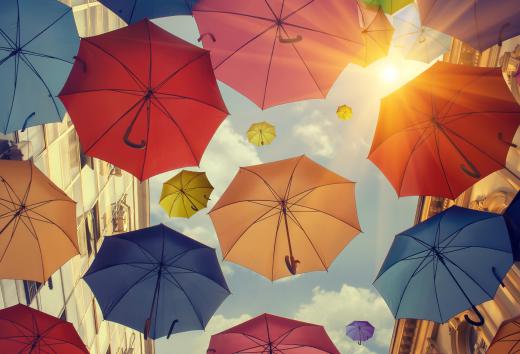
This material can be chemically created in a different way as well, namely by molding the same molecules into a different structure. In this alternate method, the acidic molecules are all at one end of the structure, and the amine molecules are all at the other. This compound is then combined into a chain of carbon atoms. In either case, the crystals that result must be soaked in water to dissolve them, then acidified and heated to create a chain that is nearly unbreakable on a chemical level.
Heating and Spinning
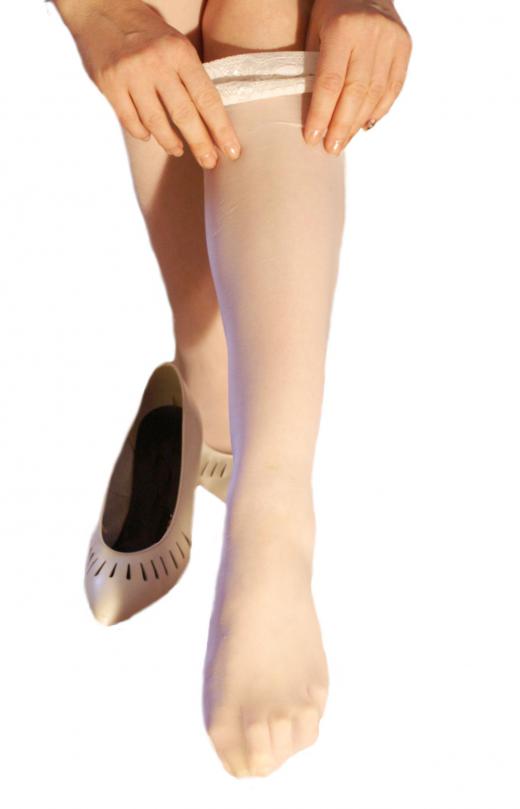
Manufacturers typically use a specially designed machine to get the polymers heated to the right temperature, then combine the molecules to form a molten substance that is forced into a spinneret, separating it into thin strands and exposing it to air for the first time. The air causes the strands to harden immediately, and once they are hard they can be wound onto bobbins. The fibers are stretched to create strength and elasticity, which is one of the material’s main benefits.
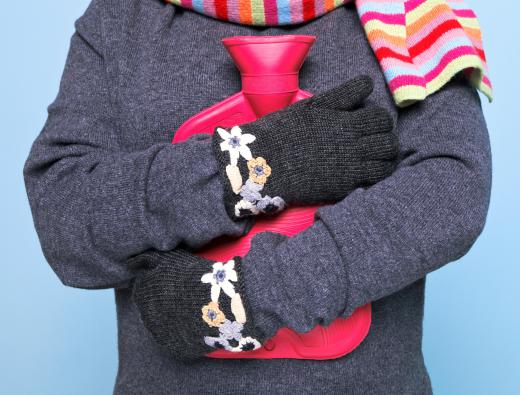
From here the filaments are unwound and then rewound onto another, smaller spool. This process is called drawing and is used to align the molecules into a parallel structure. The strands that result are multipurpose threads that can be used for a variety of different purposes. They can be woven or bound as they are, or they can be combined and further melted.
Manufacturing Process
After the material has been wound onto the smaller spool, it is ready to be turned into whatever product it is destined to become. From a technical standpoint it is nylon at this point, but not in any form that consumers would recognize, and it usually needs more refining in order for it to be useful in the market.
Most products are created by weaving or fusing the filaments together. Where materials and synthetic fabrics are concerned, the tighter the weave, the stronger and more water resistant the material will be; for plastics and other hard molded items, the hotter the temperatures for melting, the more seamless and shiny the final product. Ropes and cording usually depend on complex twisting and fusing, and most are actually made up of hundreds if not thousands of individual strands bound together to create a very tough end product.
Nylon can also be mixed with other fibers to create combination materials. When combined with cotton, it produces a resilient type of fabric that holds its shape but is soft to the touch. It can also be woven into patterns to reinforce strength, improve appearance, or meet other design requirements. In industry and military uses it can be poured into molds and used for machine parts, tire treads, and food storage containers, either in isolation or in combination with other plastics and synthetic materials.
History
These sorts of products first became popular at the dawn of the Second World War as a less expensive and more efficient alternative to silk and woven hemp, both of which were the standard parachute materials of the day. It was also useful in the war effort when it came to tire production; tires made of chemically bound polymers tended to be more durable and less prone to wear than those made from standard rubber.
Since that time the material has found a range of everyday uses, though it is still common in a number of industry and military endeavors. Synthetic clothing is very popular in many places, particularly for sports; with a lighter weave it is also the standard in stockings and hosiery. It is used in ropes and cording, and in all manner of shoes and accessories; its water-wicking properties also make it popular for use in things as different as umbrellas and synthetic wool sweaters. Though these products all seem really different from the outset, how they are made — at least in the beginning — is usually pretty uniform.
Environmental Concerns
In addition to being somewhat complex, the manufacturing process has also raised a number of environmental concerns. Many producers use crude oil to isolate the polymers, which can lead to the depletion of fossil fuels and environmental pollution due to runoff. The chemical production of adipic acid also frequently creates nitrous oxide, a known greenhouse gas, as a byproduct. This gas has the potential to erode the ozone layer and promote air pollution.